Trumpf drives efficiency with new LaserHybrid welding system
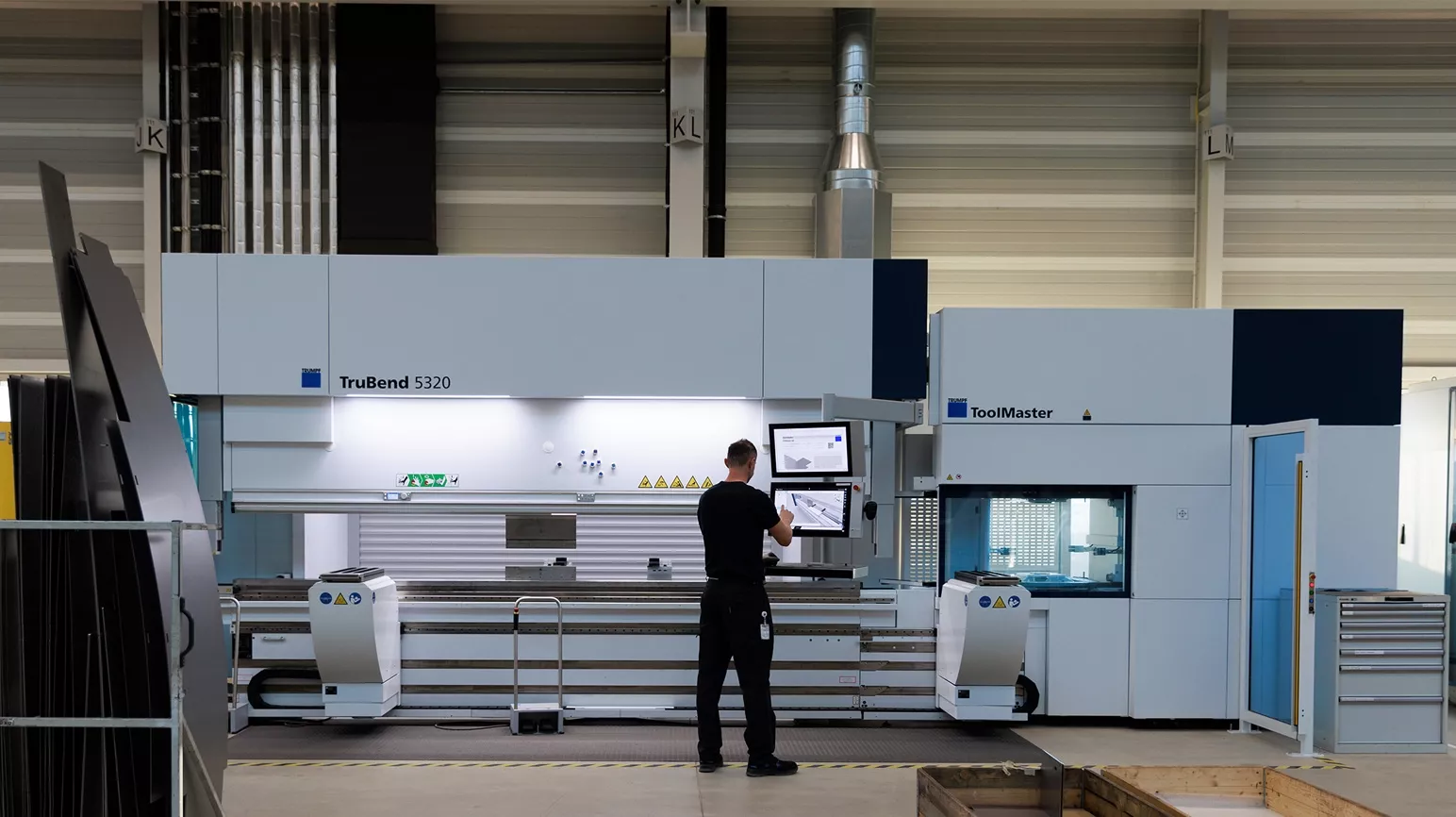
No more outsourcing thanks to cost-effective production in-house with LaserHybrid welding system
Trumpf has recorded significant growth with its bending machines in recent years and has continuously expanded its product portfolio in this segment. With its capacity utilization increasing, the company had to order the frames it uses for its multi-ton bending machines. This led to longer production times, higher costs, and limited flexibility in production. Welding was done manually at the supplier’s premises, which led to time-consuming rework. This included an energy-intensive spheroidizing process that was needed to avoid hardening in the steel, an undesirable effect of manual welding.
“During spheroidizing, the steel is heated to up to 800 °C in an annealing furnace. As it heats, the material reacts with the oxygen in the air, oxidizes on the surface, and forms rust. This means the components have to be sandblasted before painting,” explains Thomas Reiter, production manager at Trumpf. “Thanks to our new LaserHybrid gantry welding system we can skip the annealing process, which takes up a lot of time and money. We use the laser to heat the steel along the weld to between 150 °C and 180 °C, depending on the material. This reduces the cooling rate after welding so we can avoid hardening, cold cracks, and corrosion. Plus, producing in-house makes us more flexible and independent.”
By cutting out the spheroidizing process, the company is reaping both economic and environmental advantages. The energy it saves is equivalent to the electricity needs of around 270 four-person households per year, estimating an average consumption of 3,800 kWh per household.
Optimum edge fusion and reduced tendency to form pores
The LaserHybrid welding process combines a laser beam aimed at the weld with a GMAW welding process in the same process zone. The highly focused laser beam boasts an extremely high energy density and penetrates up to 10 mm deep into the steel when welding the machine frames. Immediately after the laser comes the MIG/MAG process, which fills the root pass and ensures optimum edge fusion. The heat that is also introduced gives the material time to outgas, thus preventing any proneness to porosity in comparison with pure laser welding. Depending on the sheet thickness, Trumpf uses MIG/MAG to weld up to 29 top passes.
Enhanced efficiency and material savings
LaserHybrid offers Trumpf decisive advantages over MIG/MAG-only welding. Reiter explains: “For one, we save up to four tons of welding wire and valuable working time every year, as we can skip the time-consuming process of chamfering the sheet edges, especially on thinner sheets. This keeps the weld cross-sections small and cuts down on filler metal. Secondly, we increase our productivity thanks to high welding speeds, which come as a result of the stabilized arc that LaserHybrid creates in conjunction with MIG/MAG. And thirdly, the low energy per unit length reduces component distortion.”
But there’s still a fourth aspect that also has a positive effect on consumption of filler material. The weld can be created further inwards with the LaserHybrid process, making it possible to move closer to the side parts during fillet welding and create a narrower air gap.
Fronius comes out top in evaluation
Trumpf evaluated concepts from various suppliers before opting for the LaserHybrid robotic welding system from Fronius. The aim was to find the best solution from both a technical and profit perspective. Options for moving the components—which weigh up to 18 tons and measure 4.5 × 3 × 2 m—during welding or placing them on rotary tilting positioners were quickly taken off the drawing board. These approaches would not have been able to accommodate setup parallel to production, which Trumpf preferred from the outset, or could only provide for this to a limited extent.
The company therefore decided to install a two-station gantry system with one LaserHybrid and one MIG/MAG welding robot as well as two large tilt positioners that allow components to be fed in horizontally. While one machine frame is being welded, the next one can be clamped on the free positioner.
“As well as impacting setup parallel to production, rotary tilting positioners would pose a risk of excessive tilting moments if the center of gravity of our multi-ton components were too far away from the turning or tilting axis. This would create an extremely high risk of damage to the system as well as accidents,” explains Reiter. “The only way to avoid these issues was by using huge rotary tilting positioners. But then we would have a problem with the working height. Due to the enormous size of some of the components, we would either need a trench two and a half meters deep or a machine height of at least two meters.”
All things considered, the version proposed by Fronius turned out to be the best. A number of factors were crucial here, including a sensible safety concept, the fact that using two welding robots would eliminate the need for a torch changing station, the system’s hassle-free hosepack routing, the use of WireSense for seam tracking, and ready accessibility to corner areas thanks to the slim MIG/MAG robot. Efficient production was also guaranteed, with the two tilt positioners allowing for setup parallel to production. Other plus points that put Fronius ahead included the partners’ long-standing and trusting business relationship, offline programming of welding jobs with Pathfinder, and the expertise the Fronius specialists had to offer around system technology.
No tool changes required
To avoid torch changes and all the related problems that come with transferring the hosepack, the experts at Fronius opted for a gantry system with two welding robots. Each is equipped with one LaserHybrid and one MIG/MAG welding head, both of which move overhead on a rail while operating one at a time. The LaserHybrid robot starts by carrying out root pass welding. Hard-to-reach areas and top passes are then welded using the MIG/MAG hollow-arm robot.
“The hollow arm of the MIG/MAG robot guarantees optimal routing of the hosepack. Hosepacks that are routed to the side often dangle unintentionally, which can cause damage or, in the worst case, even mean they come detached. There is also a risk that these hosepacks could get caught on components or devices, which can prevent robots from moving freely,” Reiter explains.
Sophisticated: two welding robots on a single rail
Using two welding robots on the same rail presents a particular challenge. As a solution, only one robot welds the component at a time, while the other remains in the park position. A specific program template was created for each robot, which contains all movements and travel and serves as the basis for programming the component-specific welding tasks.
The welding sequences provided by Trumpf for the acceptance parts were simulated on the digital twin during the design phase using Fronius Pathfinder and checked for feasibility. This way, the client’s welding specialists could be made aware of potential production issues ahead of time, such as areas that are tricky to access. Wolfgang Mitterhauser, a software engineer and simulation expert at Fronius, played a special role here:
“I added capabilities to the postprocessor (parser) so that it can translate special commands for the MIG/MAG welding robot, such as the use of WireSense seam tracking sensors. The parser transfers the welding programs that are created from the digital twin to the actual system. The add-ons include program sections that are tailored precisely to the customer’s system and are not included in the standard version of Pathfinder,” explains Mitterhauser.
Thanks to these add-ons, system operators can specify exactly what and how much information is transferred by the postprocessor. “The result is a welding program that meets the robot’s requirements perfectly,” adds Mitterhauser.
A collision sensor can be created in the Pathfinder so any impact between the welding torch and component is detected promptly. If the virtual monitoring system detects a potential collision, the software indicates this immediately.
Welding wire doubles as a sensor
Even if all system components interconnect almost seamlessly, there is a risk of deviations when welding layers if seam tracking sensors aren’t used. This can lead to fusion defects such as burn-through and inadequate a dimensions. Fronius WireSense uses the wire electrode as a sensor for weld seam detection and eliminates the need for optical measuring aids that could impair the welding torch’s ability to access the component. Highly precise sensing involving frequent reversing wire movements enables the different component geometries to be recognized and the relative position of the individual sheets to be determined extremely accurately. WireSense does not require any add-on torch components or calibration and maintenance work. Thanks to this innovative sensor technology, Trumpf benefits from flawless welds and lower production costs.
Intelligent control for all processes
The user-friendly HMI-T21 RS system controls are the core feature of the welding system, monitoring and coordinating all peripheral components such as the robot, welding machine, tilt positioner, and torch cleaning system. Thanks to the 3D real-time views provided by the system, Trumpf’s welding specialists can follow all robot movements live on the monitor. They have the option of choosing between preset views or creating their own and saving them to ensure a perfect display at all times.
A key element of the innovative HMI-T21 RS is its program editor, which system operators can use to define the individual program sequences, assign them to a processing station, and save them as a sequence string.
Fault, warning, and information messages are displayed in plain text in the status bar. If there are no messages, all system statuses and the program sequence are displayed, with the currently logged-in user shown in the right-hand column.
Mitterhauser says: “The status overview shows the status of all available sensors. If there is a fault message, all signals can be checked using the HMI.”
Virtual commissioning and assembly
Fronius typically installs and pre-commissions welding systems at its own site, but this wasn’t feasible in this case due to the outsized dimensions of the gantry and positioners. Given these conditions, virtual commissioning with Pathfinder was used instead. The software was used to create a virtual model—including all the signals defined in the circuit diagram and realistic kinematics. Based on the digital replica, the software engineers were able to realistically simulate the system’s operation.
Pathfinder also proved to be extremely useful during pre-inspection by the customer. Using virtual reality glasses, they were able to see all of the movement sequences of the two welding robots and tilt positioners—which can hold up to ten different components—under realistic conditions.
The relevant Trumpf employees were involved throughout the entire design phase and played a key role in the success of the project based on their suggestions and feedback.
Installing the LaserHybrid welding system on site proved to be particularly tricky. The huge dimensions of the gantry and tilt positioners, which can be swiveled up to 90°, presented a special challenge in logistical terms. All components had to be in the right place at the right time to avoid unnecessary delays. One especially challenging aspect was the night-time delivery of the two tilt positioners, which had to be transported on closed highways part of the way due to their size.
Enhanced efficiency via feasibility studies with Pathfinder
The mechanical engineering experts at Trumpf use the software for more than just programming and simulating new welding jobs—they also carry out virtual checks to determine the weldability of new components. This includes asking questions such as: To what extent is the component geometry suitable for automated welding? Can the component be adequately accessed? Is there a risk of collisions? Do parts have to be welded manually, or is it in fact necessary to change the design? These comprehensive feasibility tests and process simulations are now saving Trumpf up to three weeks of programming time.
Conclusion: The right decision
The new Fronius LaserHybrid welding system significantly improves the weld quality of the machine frames, increases the welding speed, and saves valuable working time thanks to the option of offline programming and simulation.
Thomas Reiter is very pleased with the results: “We’re now producing almost 1,500 bending machines every year. Thanks to our new robot welding system, our work has not only become more profitable but also significantly more flexible in terms of delivery times, as we are no longer dependent on buying in machine frame components. And we also have more options in terms of production capacity now.”