TransSteel
WHETHER CONTAINER CONSTRUCTION, BRIDGE CONTRUCTION OR YELLOW GOODS ...
Please choose your desired product.
Technical Data
General Data
Mains voltage | 380/ 400V |
---|---|
Mains voltage tolerance | -10% / +15% |
Welding current min. | 10 A |
Welding current max. | 500 A |
Welding current / Duty cycle [10min/40°C] | 500A / 40% |
Welding current / Duty cycle [10min/40°C] | 420A / 60% |
Welding current / Duty cycle [10min/40°C] | 360A / 100% |
Operating voltage min. | 14,5 V |
Open-circuit voltage | 65 V |
Degree of protection | IP23 |
Dimension / length | 747 mm |
Dimension / width | 300 mm |
Dimension / height | 497 mm |
Weight | 34,5 kg |
Interference emission class | A |
Length of mains cable | 5000 mm |
Maximum working voltage | 39,5 V |
The TransSteel series
High-power welding and a broad range of applications
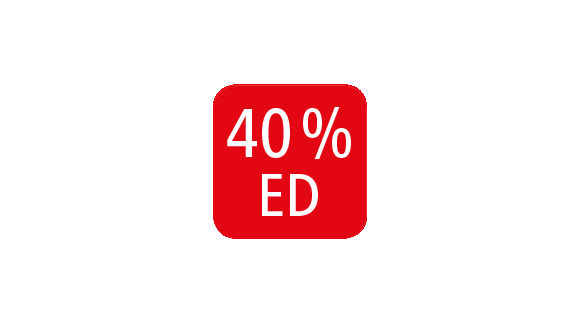
40% duty cycle
Four minutes of continuous welding at maximum output power, in other words, one minute more of productive output compared with the average in this power range.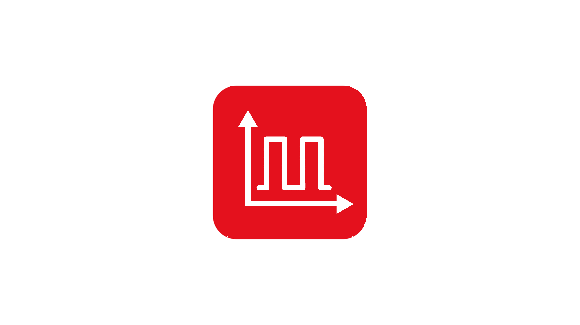
167 characteristics*
/ Steel, CrNi, AlMg, AlSi, Metal Cored, Rutil FCW, Basic FCW, Self-shielded
/ 0.8 – 1.6mm wire diameter
/ Eight different gas mixtures
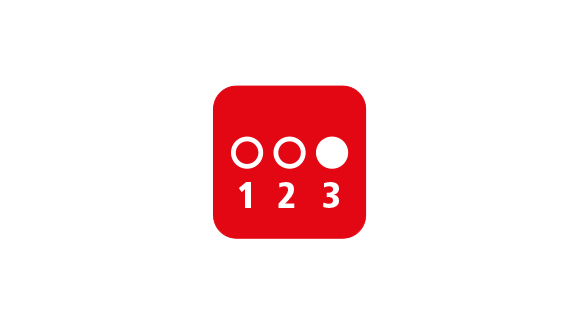
Ready to weld in three steps
The intuitive operating concept enables welders to start work straight away – no prior knowledge of the device is required. All the essential welding parameters can be viewed and adjusted on the front panel. The only parameters that have to be selected before welding begins are the gas, wire diameter and material thickness.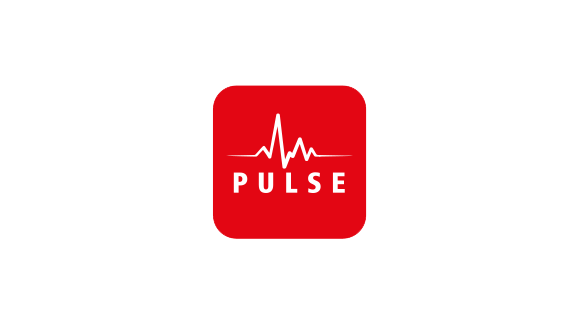
70% less rework, 30% faster welding
The Pulse function of the TransSteel 4000 und TransSteel 5000 Pulse permits faster welding speeds on thicker materials. The pulsed arc also reduces the amount of rework, as less welding spatter is generated.* Maximum number of characteristics (TransSteel 5000 Pulse), will vary depending on the version.
The MIG/MAG welding functions
Pulse
Welding controlled and fast
The new TransSteel 4000 Pulse and TransSteel 5000 Pulse mark the arrival of the pulsed arc in the TransSteel series. Controlled welding in the intermediate arc range together with optimum weldability when working with aluminum are now part of the basic package.
Special 4-step mode
For a more stable arc
The “Special 4-step mode” is particularly suitable for welding in the higher power range. In special 4-step mode, welding starts at a lower power, which makes the arc easier to stabilize.
SynchroPulse
Seam rippling for aluminum alloys
The “SynchroPulse” option is recommended for the welding of aluminum alloys when a rippled seam appearance is required. This effect is achieved by modifying the welding power between two operating points.
! SynchroPulse works in Standard Synergic and Pulse Synergic mode – but only on the TransSteel 4000 and 5000 Pulse.
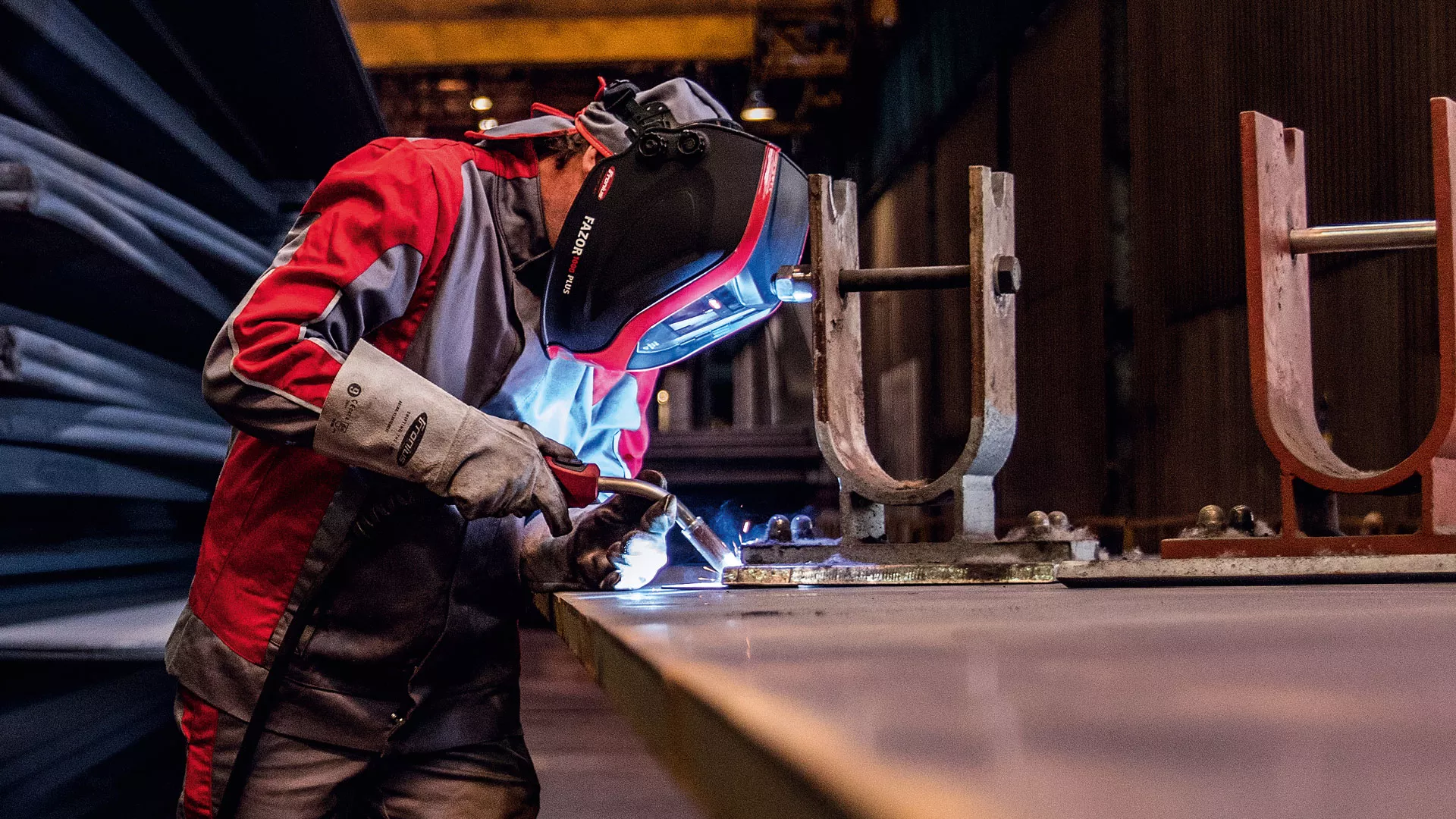
Spot and Stitch welding
With no material distortion
Spot mode enables you to place welding spots at regular intervals. As you have complete flexibility over the pause time between the intervals, spot welding is ideal for the tacking of workpieces. Stitch welding not only produces a rippled seam appearance, the low level of heat input reduces any possible material distortion when working with light gage sheets.
STEEL
Transfer technology
- Steel is the universal characteristic for quick and easy welding applications.
- Steel root is the characteristic specifically developed for root pass welding. It is characterized by particularly strong gap-bridging ability, in other words, the ability to fill wide gaps.
- Steel dynamic is a characteristic with a particularly hard and concentrated arc, resulting in high welding speeds and deep penetration.
- PCS (Pulse Controlled Spray Arc) characteristics* facilitate a combination of intermediate and spray arcs – the result is deep penetration with minimal spattering.
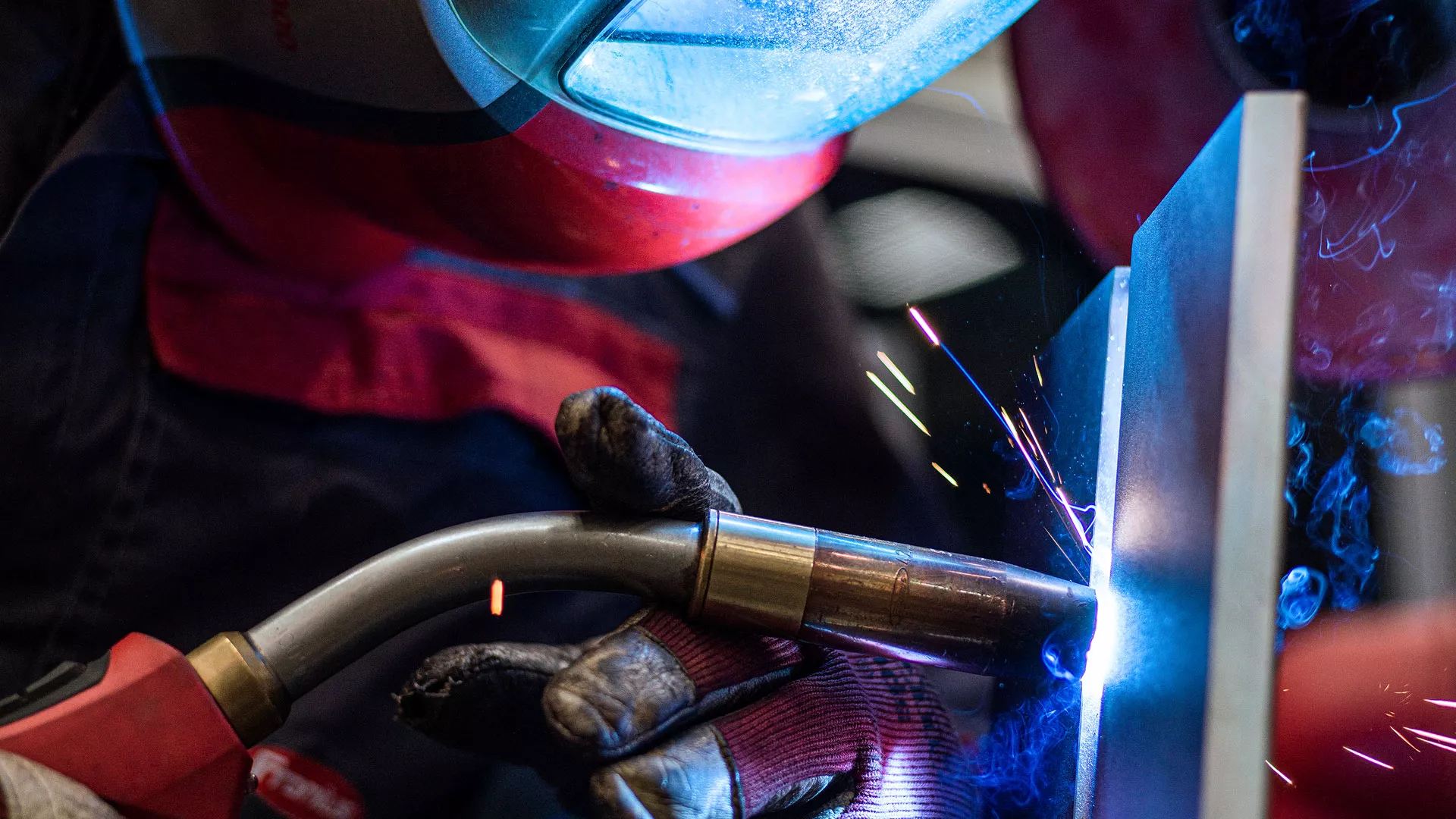
Corrections during welding
The arc length correction and arc-force dynamic welding parameters can be used to optimize the welding result.
Arc length correction
To change the arc characteristic
– shorter arc, reduced welding voltage
o neutral arc
+ longer arc, increased welding voltage
Arc-force dynamic
For influencing the short-circuiting dynamic at the instant of droplet transfer
– hard, stable arc
o neutral arc
+ soft, low-spatter arc
Pulse correction
For correcting the pulse energy of pulsed arc
– Slower droplet detachment force
o neutral droplet detachment force
+ higher droplet detachment force
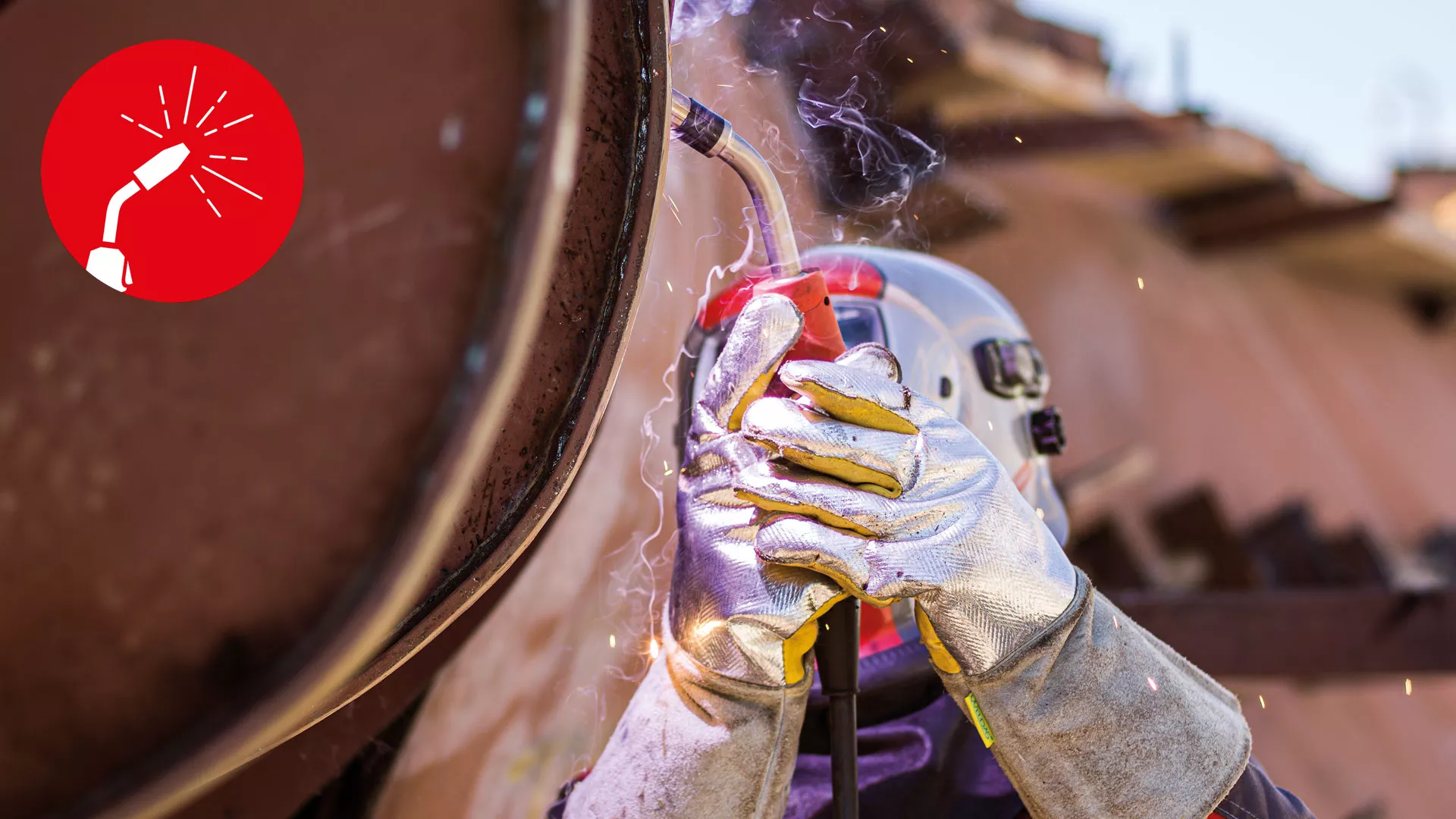
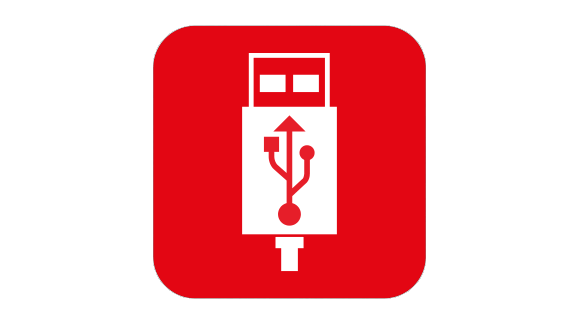
USB thumb drive export function
A USB thumb drive can be connected to the rear of the device (the stick is included as part of the scope of supply with the Easy Documentation option). The drive can then be used to export a CSV file containing welding data.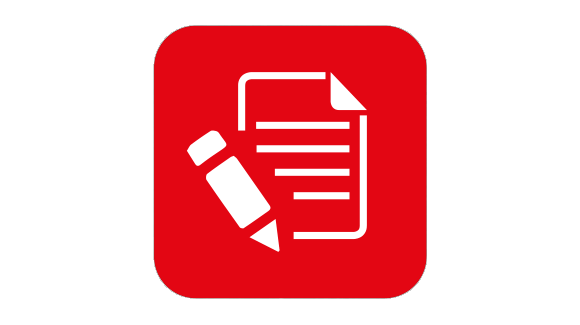
Easy documentation recording of welding parameters
Easy Documentation records the following welding parameters:
/ Power source ID// Firmware version
/ Serial number// Process (Manual, Standard, Pulse, TIG, MMA)
/ Current / voltage / wire speed in the main process phase
/ Power from instantaneous values “IP” (Instantaneous Power) - energy / time (in the main process phase)
/ Energy from instantaneous values “IE” (Instantaneous Energy) over the entire welding operation
/ Motor current (in the main process phase)
/ Time stamp hh:mm:ss when current starts to flow
/ Counter
/ Welding duration
/ Error no. when welding is terminated
/ Wire speed (metric and imperial)
/ Characteristic number
/ Operating mode (2T, S2T, 4T, S4T, spot welding, stitch welding, SynchroPulse)
/ Signature for each weld seam number
/ Template for .csv file
/ Easy Job number