Protecting against welding fume
Optional or compulsory?
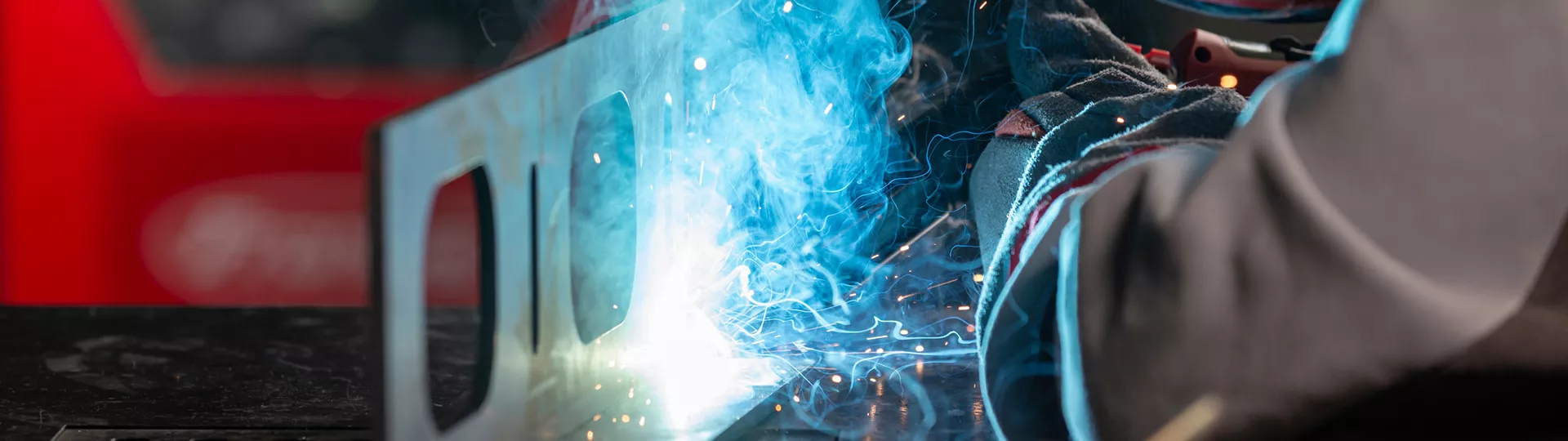
Welding fume is produced during arc welding. Often underestimated, it contains hazardous substances that not only pose health hazards but also damage genetic material. In 2017, the WHO's International Agency for Research on Cancer (IARC) classified welding fume as carcinogenic, underlining the fact that the topic of welding fume deserves our utmost attention.
What does welding fume contain?
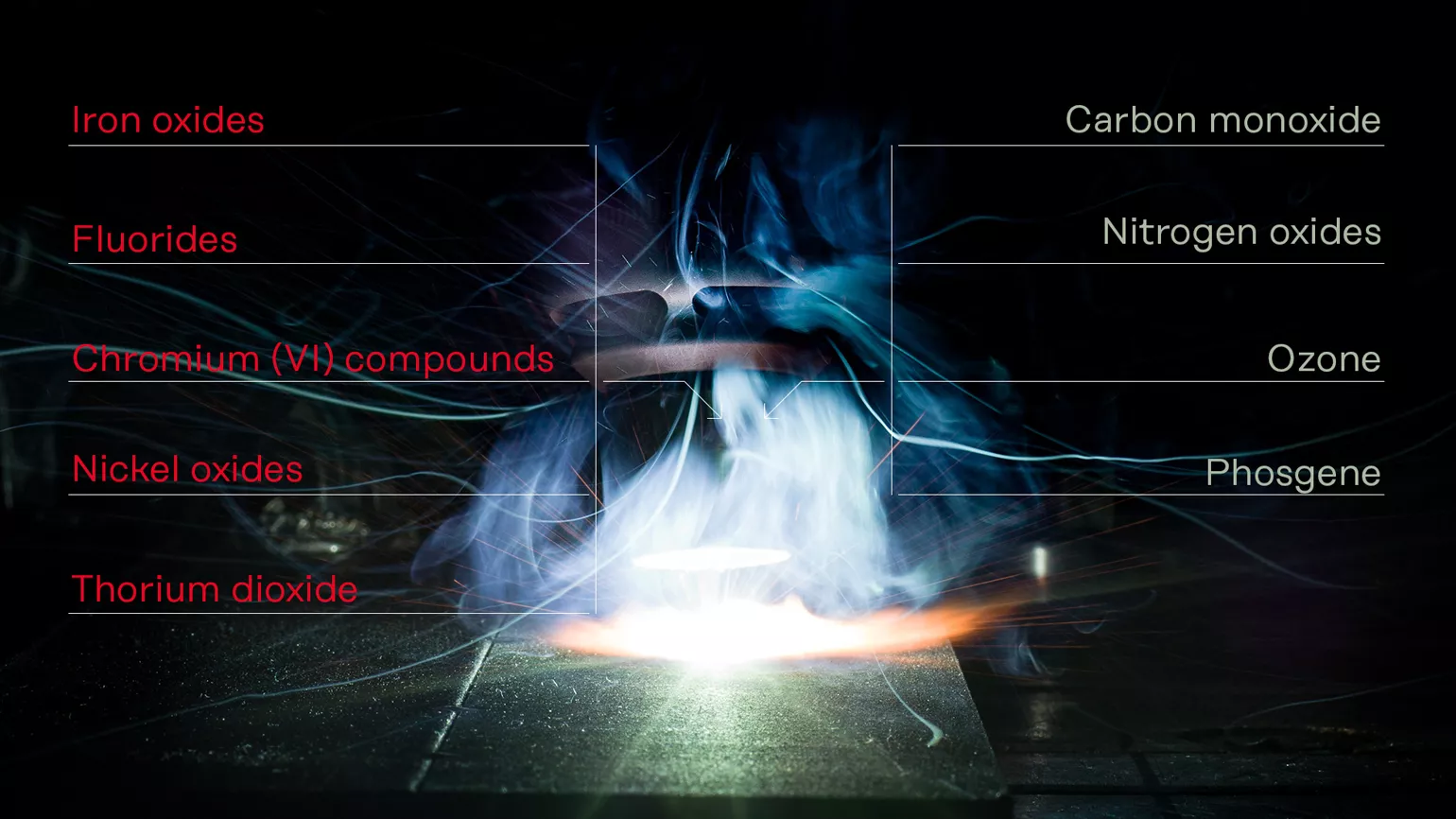
Welding fume is a mixture of particulate and gaseous hazardous substances. A distinction is made between E dust and A dust.
E dust particles are usually smaller than 10 µm and are absorbed via the respiratory tract. A dust, whose particles are tiny and no larger than about 2.5 µm, can penetrate as far as the bronchioles (finer bronchial tubes) and alveoli (pulmonary alveoli). The particles are deposited there and impede the exchange of gas from the air into the blood and vice versa. Studies show that almost all welding fume particles belong to the more dangerous A group. A considerable proportion of these are ultra-fine particles that can pass through cell membranes into the bloodstream and penetrate all parts of the body, including the brain.
In many cases, symptoms and complaints often only appear after years or decades of welding. This makes the particles particularly insidious and means that it is often too late for those affected to recover fully.
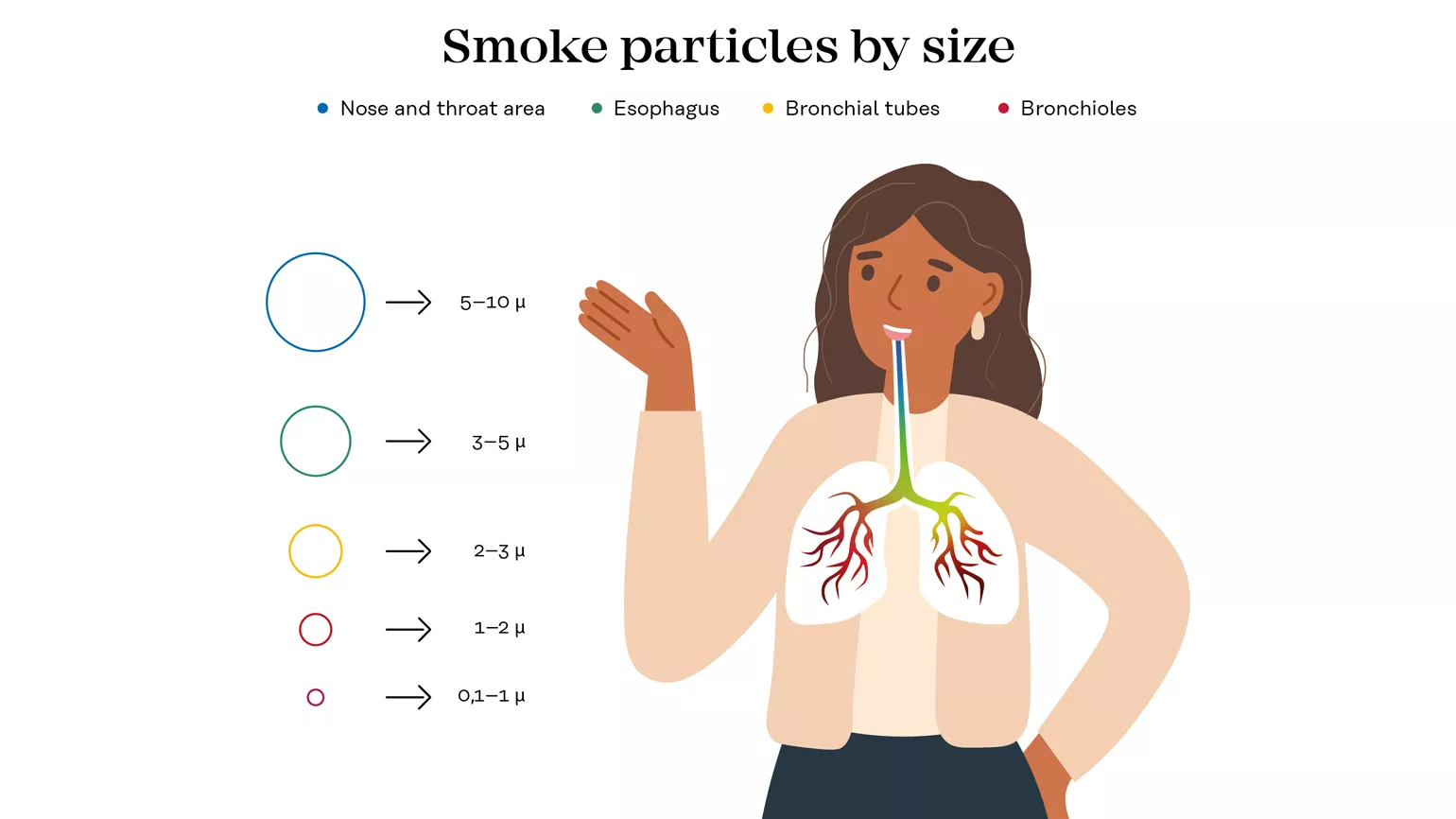
Particulate hazardous substances – examples:
Type of material | Hazardous substances | Effect |
Construction steels, asphaltic mixture | Iron oxides | Dust accumulation in the lungs (pneumosiderosis or welder's lung) |
Construction steel, galvanized | Zinc oxide | Metal fume fever (nanoparticles in the lungs cause cells to die) |
Stainless steel, high-alloy steels | Chromium VI compounds, nickel oxide | Carcinogenic effect on respiratory organs |
Common construction steels (approx. 2% manganese content) High manganese steels (up to 30% manganese content) |
Manganese and its compounds | Irritates the respiratory tract, damages the nervous system, leads to Parkinson's-like symptoms |
Aluminum alloys | Aluminum oxide | Aluminosis, causes functional lung tissue to change, leading to non-functional tissue |
(Source: kemper.eu)
Gaseous hazardous substances – examples:
Arises during... / is part of… | Hazardous substances | Effect |
Autogenous process, especially with large flame | Nitrogen oxides (NOx) | Irritation of the respiratory tract and shortness of breath, damage to pulmonary alveoli |
Autogenous process | Carbon monoxide | Hinders oxygen uptake of the blood, leading to a lack of oxygen in the body's organs. Dizziness, faintness, headache |
Shielding gas component | Carbon dioxide | Dizziness, headache, shortness of breath, increased respiratory rate and volume |
(Source: kemper.eu)
Limit values
Some countries have introduced limit values for A particles. These values vary from one country to another. The Netherlands have set a limit value of 1 mg/m3, which is the strictest limit. In countries such as Australia, Austria, or the USA, the limit value is 5 mg/m3.
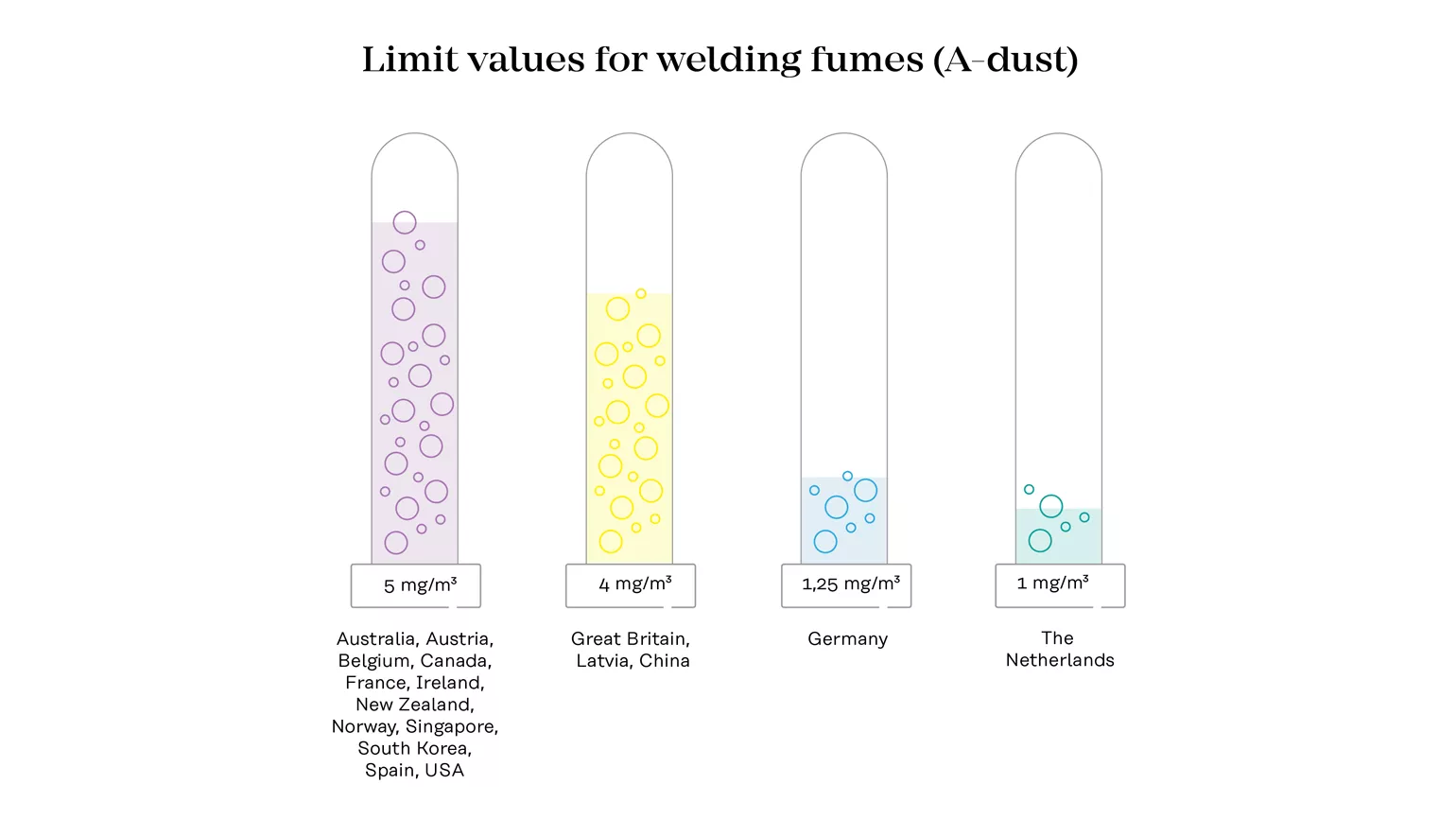
Effectiveness of protective measures
As part of a study conducted with Aachen University in Germany, we measured emissions and investigated the effectiveness of various protective measures on the basis of practical welding parameters.
The study reveals that it is impossible to comply with the limit values set by legislators, even if you use modern, innovative welding processes and optimize all welding parameters.
The bottom line is that only a targeted combination of different protective measures based on the STOP principle is actually effective. This way, all people in the immediate vicinity of welding work are protected in addition to the welders themselves.
The STOP principle
Nowadays, occupational health and safety does not just involve a selection of responsible companies setting a good example. Employers in many countries have been obliged to introduce effective protective measures and ensure that they are followed.
The basic rule for occupational health and safety is that "dangers must be eliminated at source". The STOP principle offers guidance for occasions when this is not completely possible or not possible at all. It describes the order of priority of the individual protective measures – the so-called hierarchy of measures. It is one of the most important cornerstones of applicable occupational health and safety.
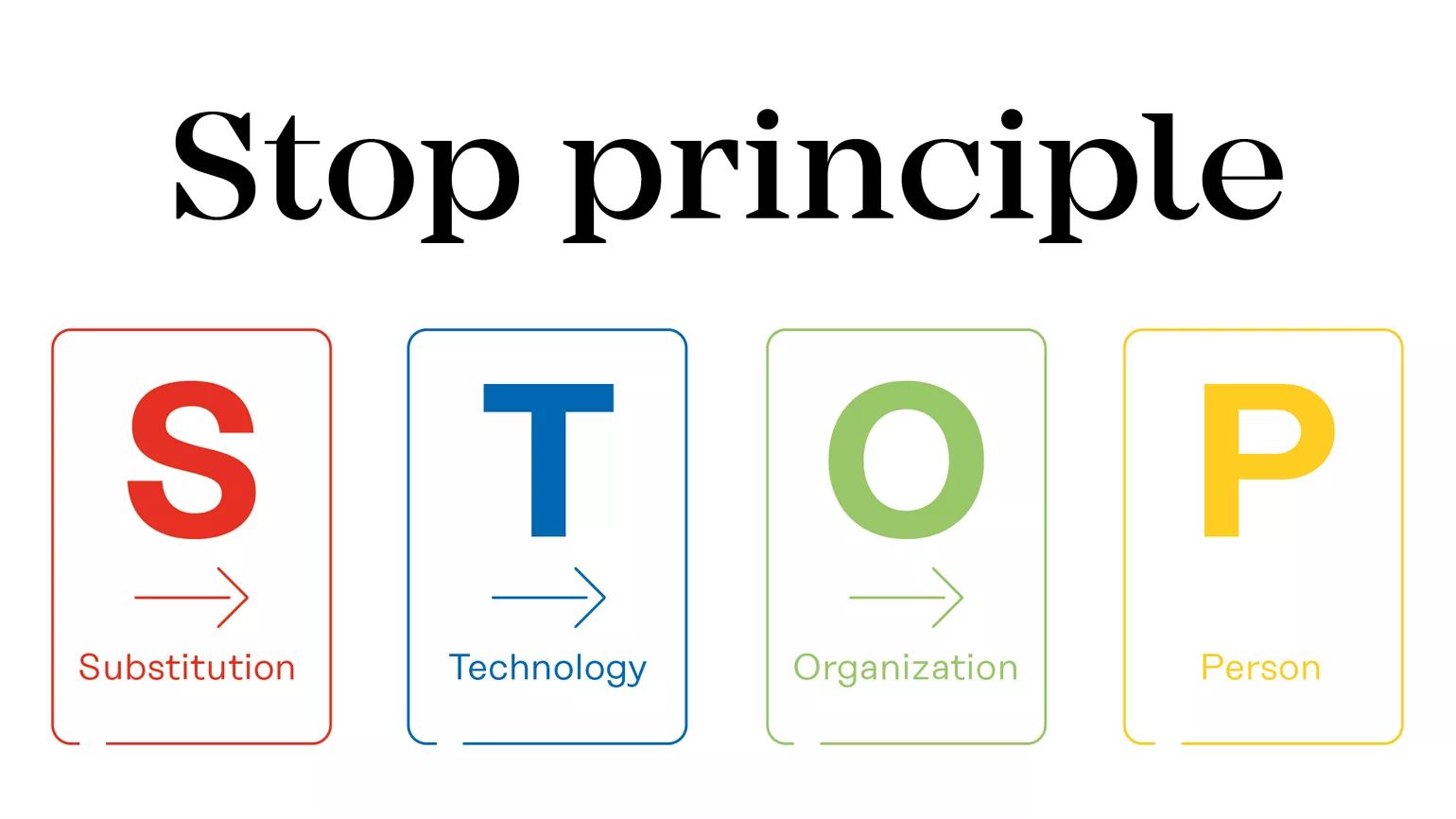
Substitution
Replace a dangerous process with a harmless one
Although it is not usually possible to select a low-emission base material, the welding procedure and its processes can be improved. Modern functions such as PMC (Pulse Multi Control) or LSC (Low Spatter Control) stabilize the arc, reduce spattering, and therefore produce less welding fume.
Technical measures
Shield the danger
Automated welding
The latest developments make automated welding cost effective even from batch sizes of 1. Examples include cobot welding cells with glare protection and extraction. They are intuitive to operate, do not require any programming knowledge, and, on top of this, enable rapid clamping and changeover of components. This type of closed welding cell provides effective protection against UV radiation and welding fume.
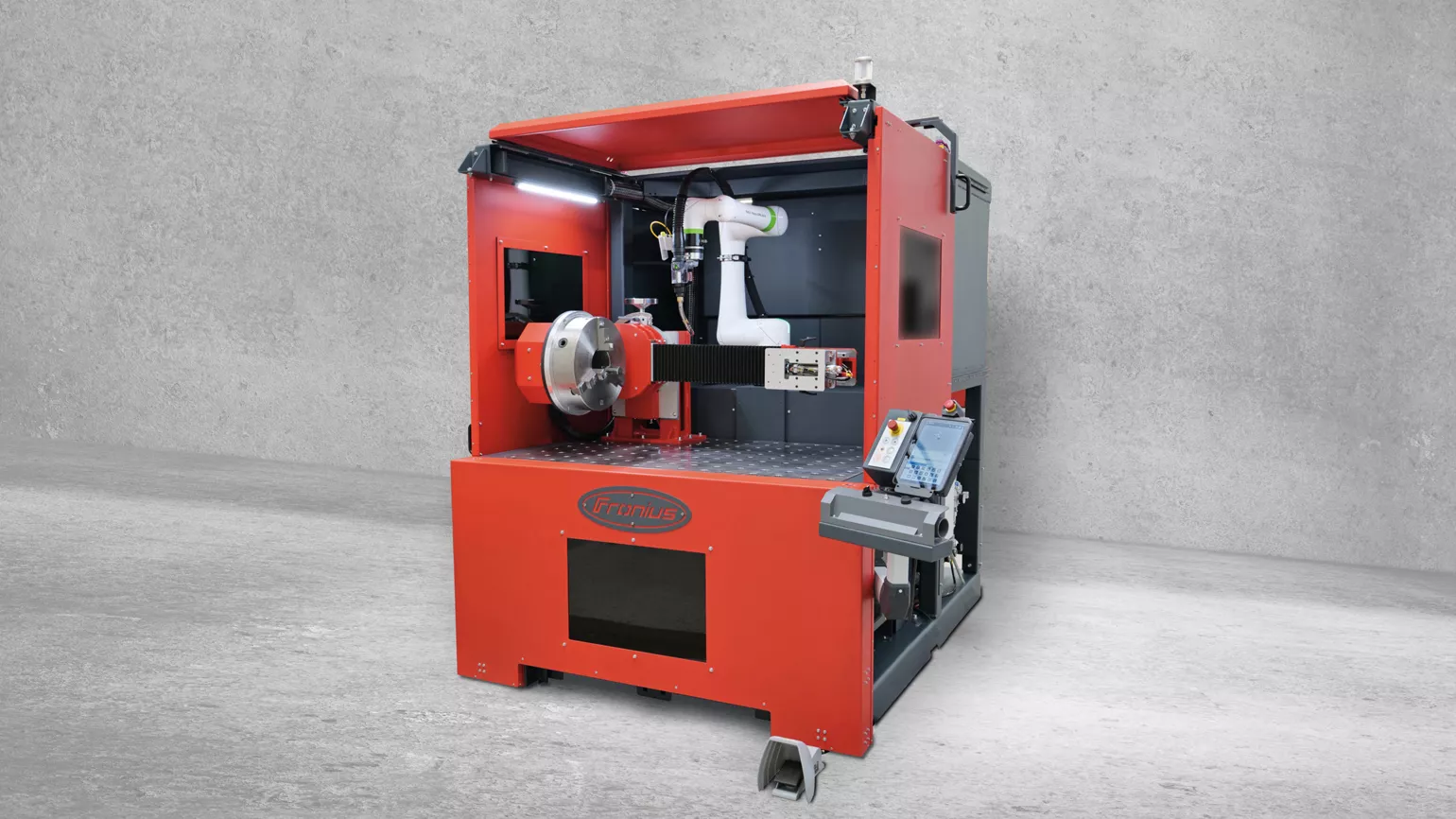
Fume extraction torches
Fume extraction torches eliminate welding fume directly where it is produced even before it is able to spread. This protects everyone in the surrounding area in addition to the welders themselves. But be aware that the performance of fume extraction torches is restricted due to their limited volumetric flow during processes that produce a particularly large amount of welding fume.
Extraction systems
These are available as low-vacuum and high-vacuum systems. Low-vacuum extraction systems have a flexibly adjustable extraction arm along with an extraction hood. If this is positioned correctly over the weld being produced, not only are welders protected, but all other people present in the workshop, too. In combination with fume extraction torches, high-vacuum extraction systems are particularly effective where lower welding powers and emissions are involved. In these cases, the fume spreads directly around the weld and can be extracted perfectly with the fume extraction torch.
Organizational measures
Limit the impact of a danger
- Reduce the exposure time: It is important here to shorten the period of time in which the welder is exposed to welding fume, for example, by using welding processes that allow higher welding speeds.
- Clean the base material before welding: Various impurities as well as oxide layers such as scale, which intensify the formation of welding fume, may be present on the metal surfaces. Cleaning the surfaces carefully will help here.
- Hall ventilation: This keeps the ambient air in the workshops clean and is used when extraction at the source is no longer sufficient.
- Ventilate regularly: Fine welding fume particles are virtually invisible to the naked eye. If they are not extracted or ventilated, they remain unnoticed in the ambient air. It is therefore important to ventilate regularly in cases where it is not possible to use extraction and ventilation systems. Ideally, open windows and doors immediately after welding, allowing the air to pass through properly.
Use personal protective equipment
This is used when all other measures cannot completely prevent the release of hazardous substances. A typical example:
- Welding helmet with powered air-purifying respirator (PAPR). These systems provide maximum protection against welding fume and remove up to 99.8 percent of captured welding fume particles from the air. Their only drawback is that they just protect the people wearing them and not other people in the area.