Using downtime for preparation: performing maintenance work during periods of shutdown
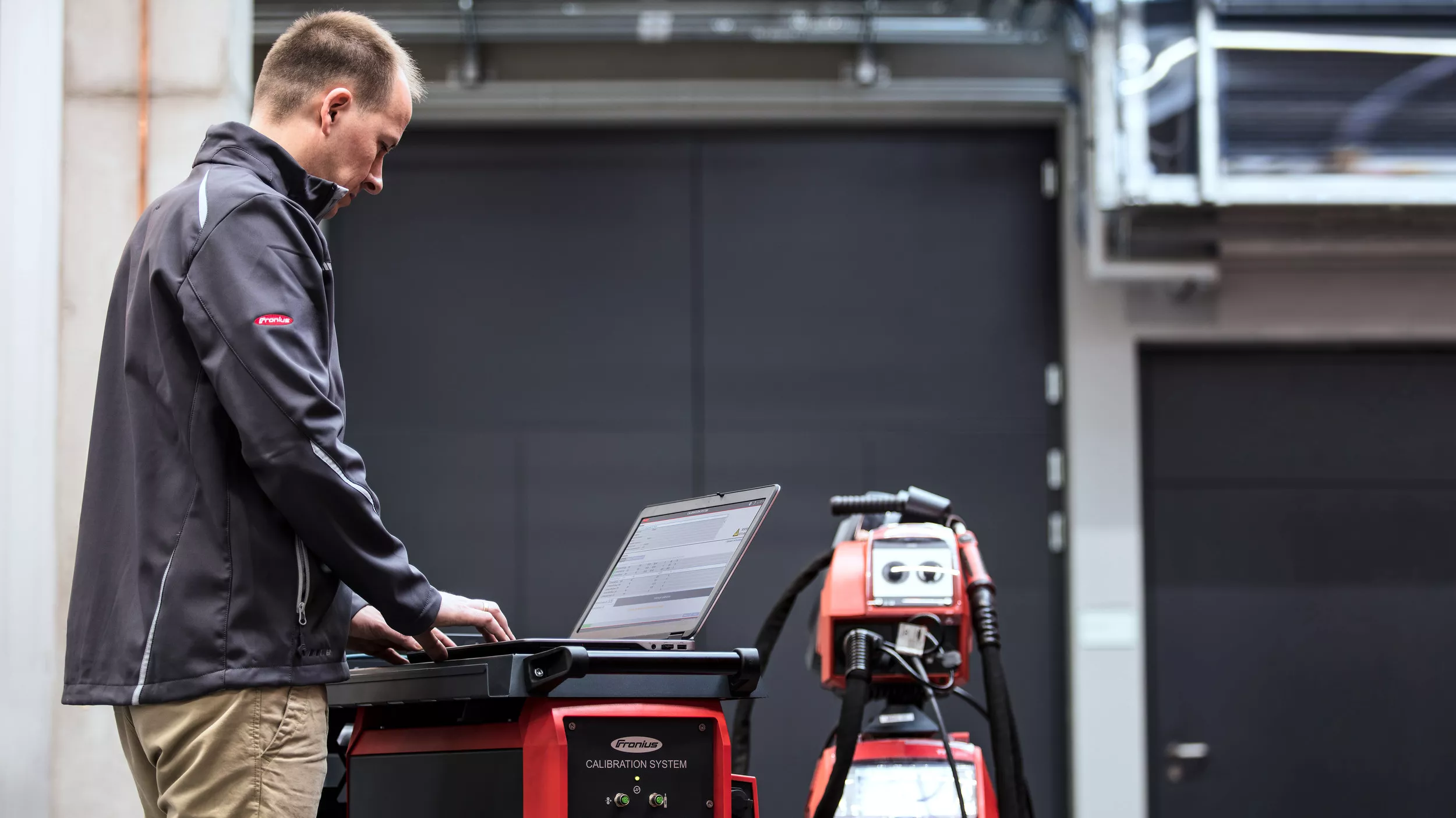
Calibration: guaranteed quality
In order to achieve long-term high-quality and consistent welding results using the welding system, regular calibration is required. In some cases, companies are also subject to standards such as EN 1090 and are therefore legally obligated to carry out regular calibration work.
To do this, the welding system is connected to a calibration station. The calibration software measures voltage, amperage, and wire speed. If the actual values on the machine differ from the set values in the standard and this deviation exceeds the tolerance range, the service engineer can perform a readjustment. In terms of quality assurance and product liability, production can recommence without any problems.
Learn more about calibration work in the blog post.
Further details on the range of services can be found on the Fronius website.
Maintenance: optimum system availability
Regular maintenance of production facilities minimizes repairs and downtimes. In addition, regular cleaning and testing of the welding system ensures that the system retains its value.
Fronius offers a range of maintenance packages that can be adapted to the customer’s needs as required. Maintenance costs are therefore transparent and easy to calculate.
More information on maintenance packages can be found on the Fronius website.
Safety inspection: protecting employees
A safety inspection is required by law in some countries and is intended to protect company personnel. This inspection of the welding systems should be conducted annually to ensure safety in the workplace. This also prevents production downtime.
Fronius always carries out safety inspections in accordance with current regulations. This includes a visual inspection, an electrical test, function test, documentation, and an inspection sticker. It is highly recommended to combine the safety inspection with the calibration of the welding systems. This saves time and money.
More information on the safety inspection can be found on the Fronius website.
Process and parameter optimization: cost savings
Calibrate, maintain, inspect – all of this is required for system maintenance. Fronius experts also check welding systems with regard to process optimization, i.e., whether the selected parameters are optimally adapted to individual objectives. System adjustments are made depending on the test results. Possible objectives are to increase the performance of the welding process, improve seam quality, reduce costs, reduce rework, and optimize cycle times.
Details on process and parameter optimization can be found on the Fronius website.
Note:
Due to the current global crisis situation, services can only be performed on the customer’s premises in compliance with local health and safety regulations. Nevertheless, Fronius specialists are on hand to help as far as possible.
For more information, please contact your local Fronius Service Partner.