Aluminum welding with TPS/i
Spencer Manufacturing, United States

Contact
Downloads
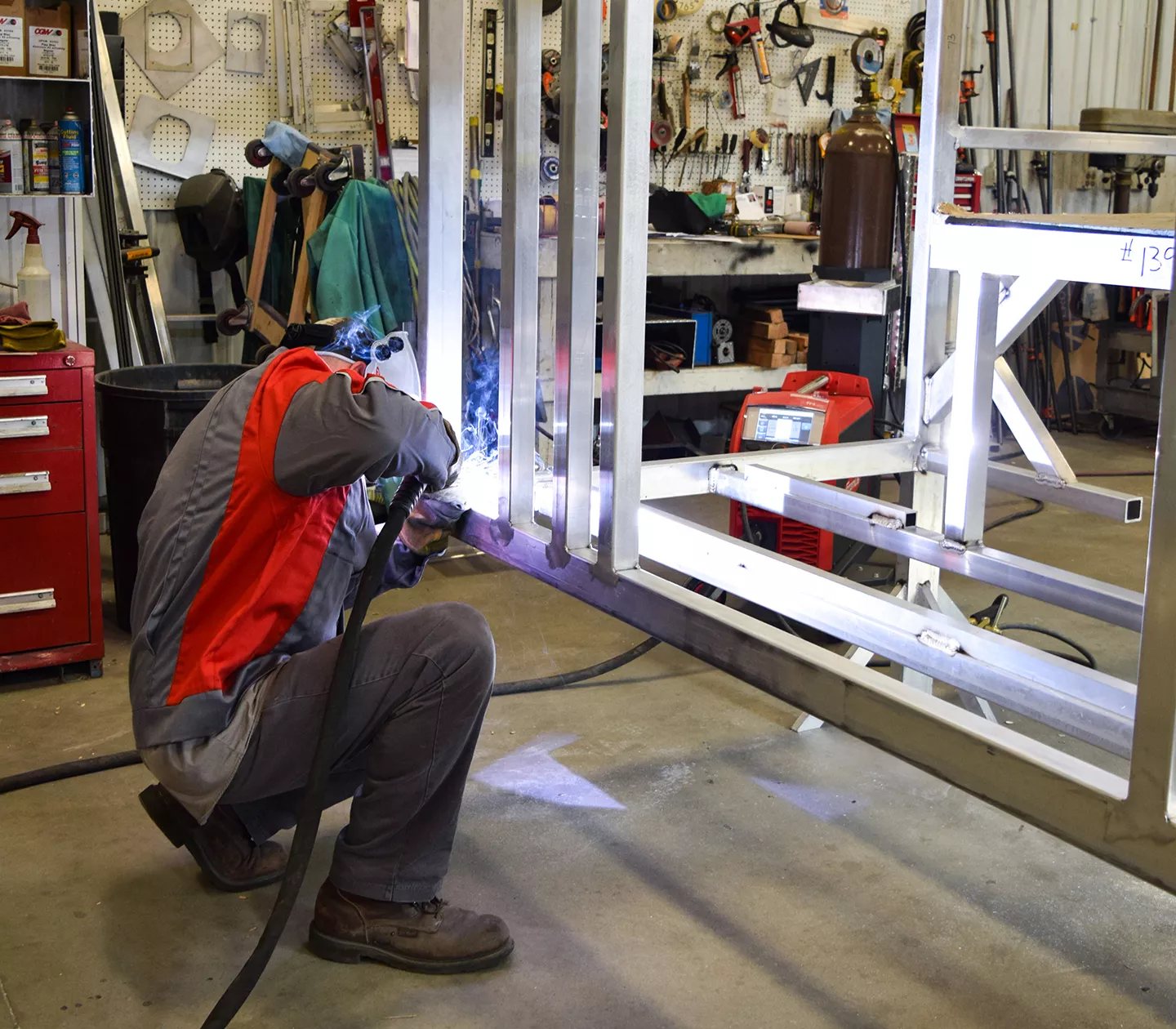
Quote from one Spencer employee when talking about the TPS 320i with Synchropulse
“It’s one of those tools that, once you have it, you don’t know how you made it without it.”
REQUIREMENT
Welding aluminum has a reputation for being difficult to work with. Most of the time to get a quality weld with solid penetration, it takes a lot of time in rework. For Spencer Manufacturing (manufacturer of fire trucks), welding two sidewalls into position with a solid paintable edge was taking 16 hours. The Spencer family has been building custom fire trucks for almost 30 years. With that much experience, they knew there had to be a better way to get the seam they needed while meeting customers’ expectations and budgets. With the MIG equipment Spencer previously used, the actual welding took only minutes compared to the hours of grinding, routering and sanding to get a solid, paintable corner. Even with all this work, the company wasn’t highly confident about each of those welds.
SOLUTION
With the Fronius TPS 320i Compact welding system, they now can do both walls in four (4) hours instead of 16 hours. For the specific application the company is primarily using Synchropulse (a pulsed gas metal arc welding (GMAW) process). The most significant time savings was the reduction of rework they used to have to do. Less spatter, proper penetration and a good bead profile results in a solid seam which requires little to prep for primer and paint. The overall result saved 12 hours of production time per fire truck allowing them to build more fire trucks each year.