TPS/i Robotics
Efficient and accurate
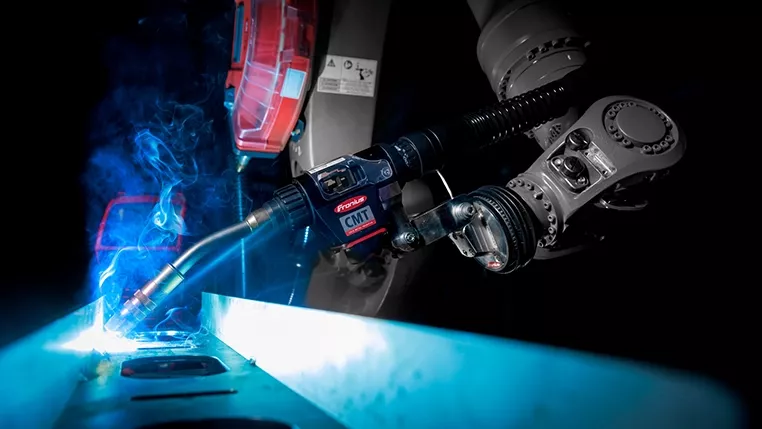
Robotic welding: Where innovation and outstanding performance come together
We combine a culture of innovation and customer focus in a unique way:
since the 1990s, we have been revolutionizing the industry with pioneering solutions for robot-assisted welding.
By making good things even better, we not only develop welding systems, but also create solutions that expand the possibilities of automated robotic welding. We achieve a high quality weld thanks to intelligent control and a stable arc.
Software solutions allowing easy integration plus welding data recording and analysis complete our systems.
The advantages for you
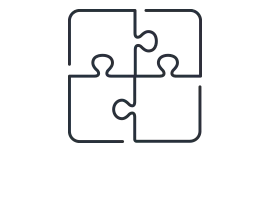
Transformation for maximum efficiency
Converting a manual welding machine to a robotic welding system is quick and easy. All common standard interfaces are available.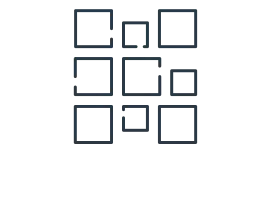
Overview of production
WeldCube is a central tool that networks and monitors all welding machines in production, so you can fulfill any documentation requirements. Plus, the component-related evaluation of process data allows you to optimize your production line and realize its full potential.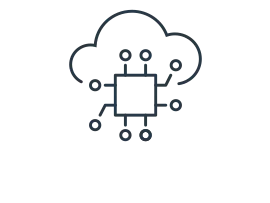
Easy upgrades
The system’s functionality can be quickly expanded using software options and welding packages.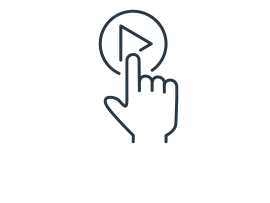
Ready for use in no time
The TPS/i facilitates quick and straightforward communication with robots from different manufacturers, ensuring rapid integration of the welding system.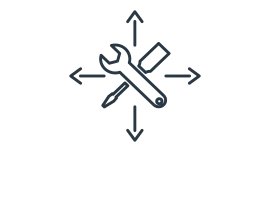
Multipurpose for any application
Our welding system is versatile. No matter whether you’re working with aluminum, CrNi, or steel, the TPS/i ensures optimum welded joints. With our solutions, you remain flexible and fully equipped for future challenges. The result: perfect welds with excellent support.Downloads
TPS/i Robotics: Automation made easy
Challenge
ALTEC uses modern production methods and automated robotic welding cells. In 2018, an aluminum framework part was transferred from manual production to robotic welding to ensure a high welding speed and process reliability. Due to high failure rates, an existing robotic system was equipped with new welding technology to perform all position welds in one process and achieve an outstanding weld appearance.
Solution
The Fronius TPS 320i high-tech welding system platform is used on both robotic welding systems. Both welding machines are also equipped with the complete CMT hardware.
Products in use
TPS 320i CMT
System solutions
The TPS/i is one of the most state-of-the-art welding machines and, with its huge power capacity of up to 600 A, it meets the highest demands for steel, stainless steel, and aluminum applications. The modular design of the device platform enables optimal integration into various robotic welding systems. The structure of the system means that custom adaptations can be made, including both Push and PushPull systems.100% compatible with our welding packages
Thanks to our modular welding packages, custom solutions can be developed quickly and efficiently. The TPS/i can be flexibly adapted to meet specific welding requirements. The standard or pulse processes are available as basic packages, or advanced welding packages such as LSC, PMC, or CMT can be used for particularly demanding welding tasks. The optimum interaction of welding processes with intelligent penetration and arc length stabilizers makes production faster and of higher quality, which reduces rejected welds to a minimum.
CMT, the stable arc with reversing wire motion
Cold Metal Transfer: The highly specific type of droplet detachment minimizes heat input. Reversing wire motion also ensures low spattering.
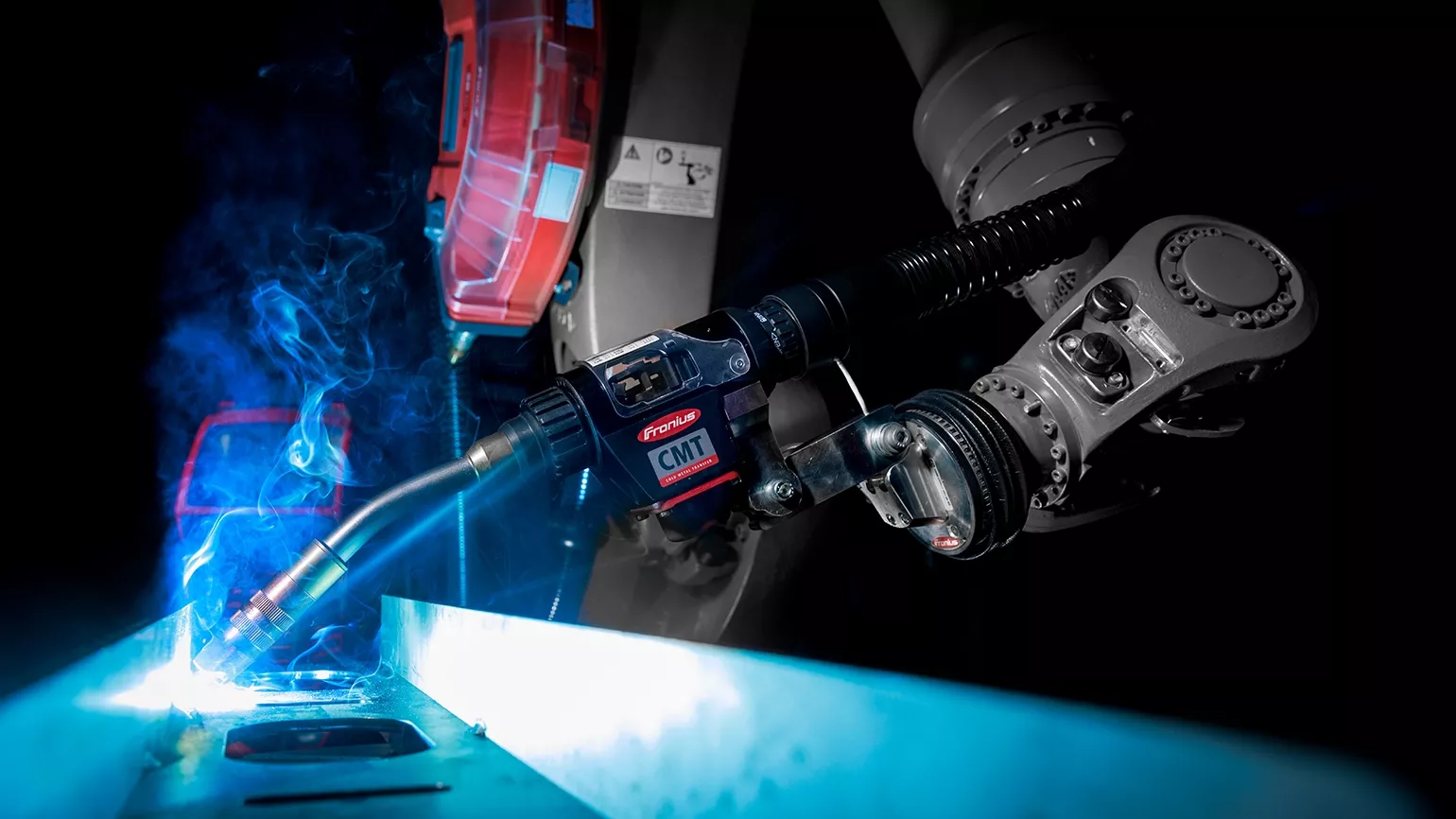
The optimized PMC pulsed arc
With its optimized pulse characteristics, Pulse Multi Control provides high-quality welds at high welding speeds.
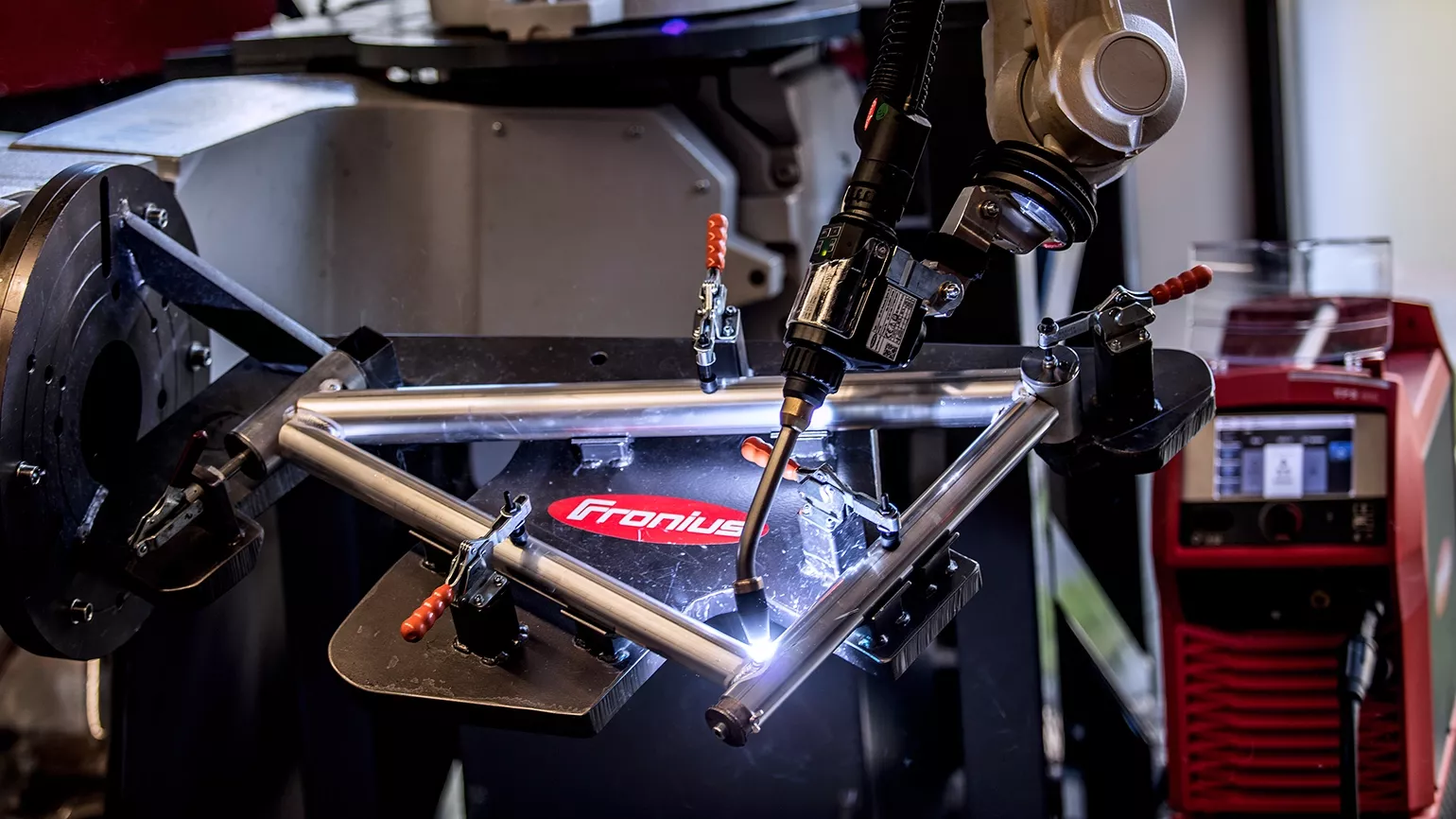
The modified LSC dip transfer arc
Low Spatter Control: Soft reignition represents a significant difference compared to the standard dip transfer arc. Here, the short circuit is triggered at a low current level.
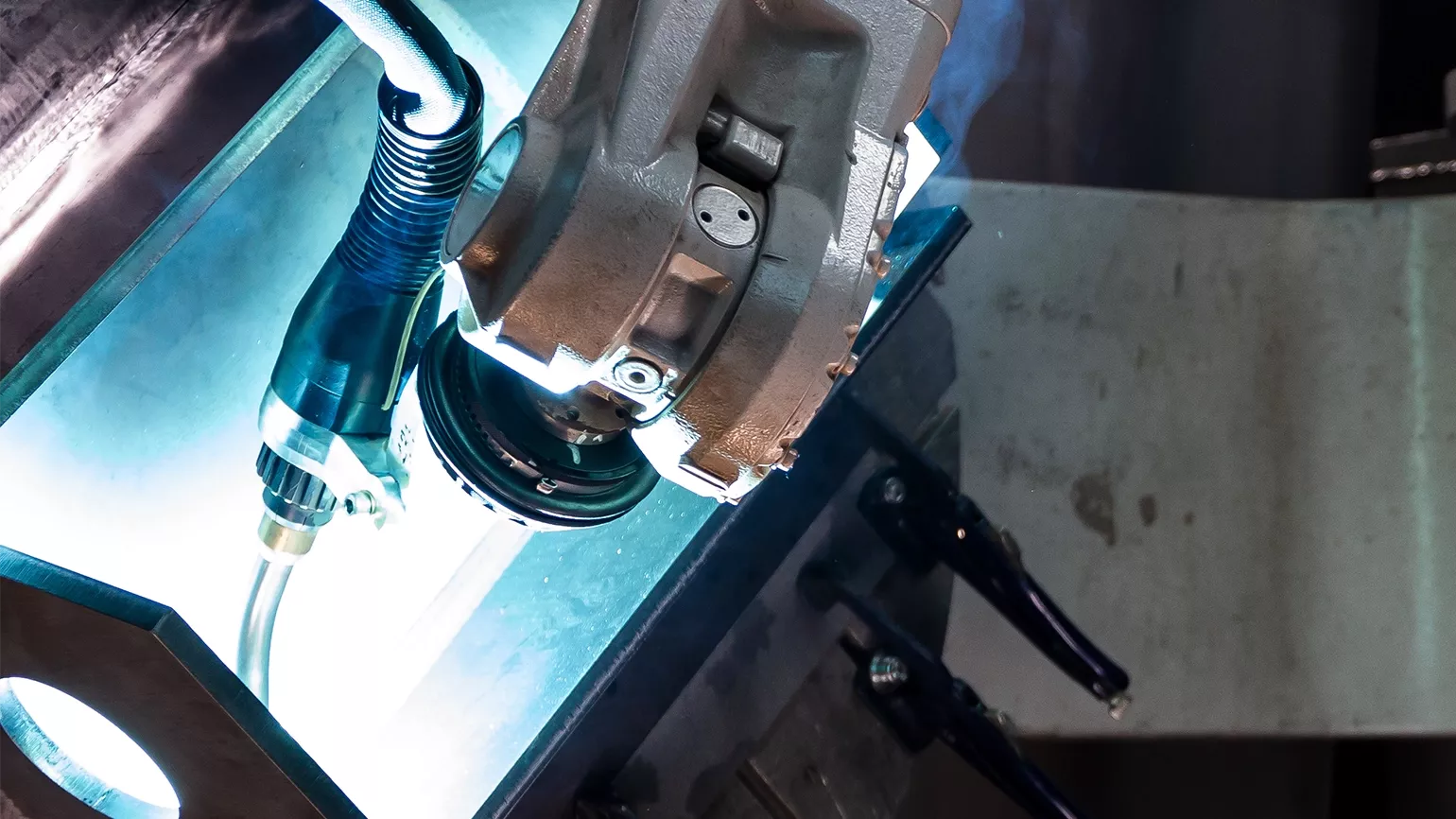
Faster, more accurate welding with assistance systems
One particularly important factor in robotic welding is increasing the efficiency and quality of welding tasks. Our assistance systems such as TeachMode, TouchSense, WireSense, and SeamTracking further optimize the welding process by saving time, preventing collisions, compensating for tolerances, and increasing process reliability.
WireSense
Reduces time-consuming rework. The wire electrodes measure component deviations such as varying air gaps or clamping tolerances and transmit the values to the robot.TeachMode
For the efficient programming of welding positions on the robot. The wire is retracted before a collision can occur with the component, preventing the wire from bending. The set stickout remains unchanged.SeamTracking
Compensates for clamping and component tolerances during the welding process, thereby preventing weld faults as well as unnecessary rejects.TouchSense
Developed for welding fillet welds and prepared butt welds. The wire or gas nozzle scans the component in detail and transmits the start and end position to the robot, which calculates the exact seam path.
ShortCircuitDetection
The welding system detects accumulations of welding spatter inside the gas nozzle. Cleaning routines can be optimized and process reliability increased.
SlagHammer
Start welding safely and cleanly. Before welding starts, slag that has formed on previous welds is chipped away by reversing wire movements.
SFI – spatter-free ignition
The spatter-free ignition with SFI ensures both safe and clean ignition.
Software solutions for TPS/i Robotics
WeldCube Premium
Alongside productivity and time savings, transparency and safety are also common requirements in welding production. The recording of welding data for documentation and analysis purposes can be of invaluable assistance, and is precisely where the WeldCube welding data management software comes to the fore. The premium version provides you with a convenient, centrally located data documentation resource with intelligent management, statistical, and analysis functions, including graphical evaluations.Central User Management
Central User Management enables quick and easy user administration, replacing a separate set-up directly on each device and thus saving a lot of time. It then becomes a simple matter to automatically transfer user rights to new devices.WeldConnect app
WeldConnect makes it easy for welders to find the right parameters for their manual welding task. The app helps determine the correct settings at every step and allows the stored welding parameters to be transmitted wirelessly to the connected welding machine. It can also be used to scan the part, series, and weld numbers for component-specific data documentation and perform user identification with NFC-enabled cellphones.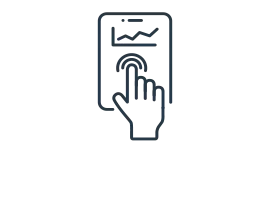