Breaking a world record with technology from innovation leader Fronius
SAM Stahlturm- & Apparatebau Magdeburg GmbH
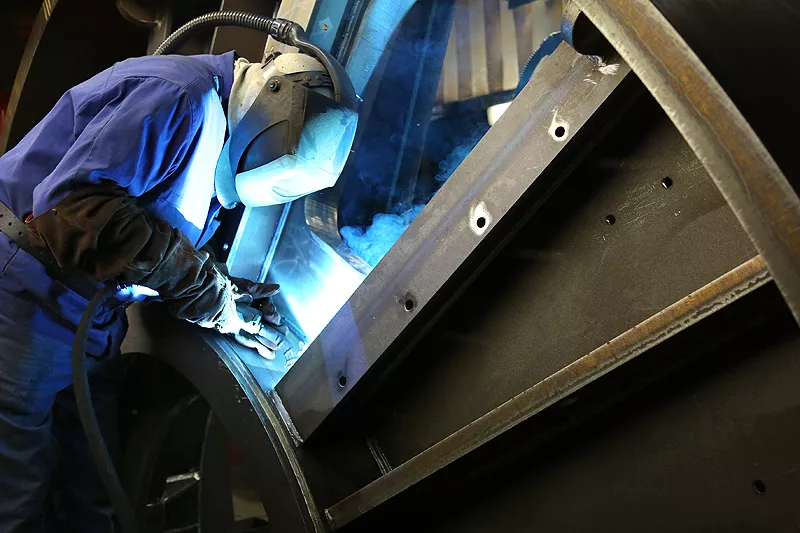
Downloads
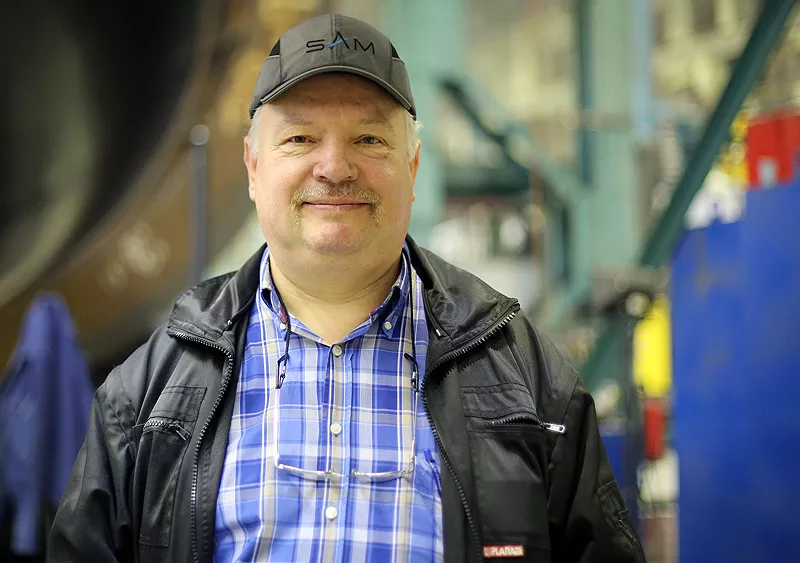
Dieter Ohms, Head of Quality Assurance at SAM
“When it comes to gas-shielded arc welding, we rely almost entirely on solutions from Fronius in all areas of production.”WELDING CHALLENGE
In wind turbine manufacturing, welding constitutes approximately 90 percent of all the work. Together with its sister company, MAM Maschinen- und Anlagenbau Magdeburg GmbH, SAM processes over 70,000 tonnes of steel per year. While submerged arc welding is primarily used when constructing the tower, gas metal arc welding is the most common process for making the stator rings, disk rotors and stator carriers. For producing the rotor blades, gas shielded arc welding is predominantly used to join aluminium structures that enlarge the wind-exposed area on the trailing edge of the blade.“We have been extremely satisfied with the technology and service from Fronius, right from the word go.” Dieter Ohms, head of quality assurance at SAM
SOLUTION
For manual or automated welding of steel or aluminium under shielding gas, SAM turns to the innovative technology from Fronius. The quality of the Fronius products has impressed the company, so much so that around 160 power sources, mainly from the TransPuls Synergic 5000 and TransPuls Synergic 4000 series, are in daily operation at SAM. The developments from Fronius, such as continuously adjustable welding power, innovative welding programs, the high quality and accessibility of the installed components, set the products apart. The structural-steel fabricator also reaps the benefits of the preventive maintenance measures provided by Fronius distributor MSS Magdeburger Schweißtechnik GmbH, which ensure permanent availability of the devices resulting in considerable cost savings.